10 Must-Have Skills for Maintenance Technicians
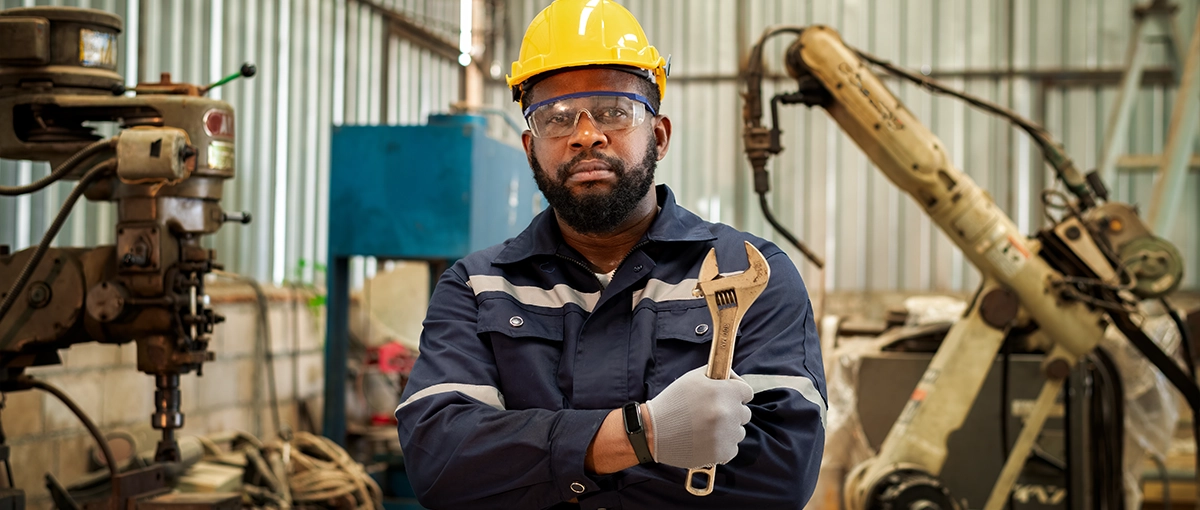
Maintenance technicians keep industrial operations running smoothly, and their skills directly impact equipment uptime and workplace safety. Those who purchase industrial supplies know that well-trained technicians save time and money by preventing costly breakdowns. Here’s a detailed look at ten essential skills that define an effective maintenance technician in demanding industrial environments.
Mechanical Aptitude
Understanding how machines work is fundamental. Maintenance technicians must recognize components, from gears and belts to hydraulics and pneumatics. This skill goes beyond textbook knowledge. It requires hands-on familiarity with equipment, including the ability to identify worn parts, understand mechanical tolerances, and anticipate failure modes. This helps technicians decide when a repair is enough and when a replacement is necessary, optimizing machine lifespan.
Electrical Knowledge
Industries rely heavily on electrical systems. Maintenance technicians need to interpret wiring diagrams, test circuits, and troubleshoot electrical faults. This skill includes familiarity with motor controls, sensors, relays, and programmable logic controllers (PLCs). Recognizing the subtle signs of electrical issues—like inconsistent voltage or unusual current draw—can prevent major failures or hazards. Being versed in safety standards for electrical work is equally important to avoid accidents.
Problem-Solving Skills
Machines rarely break down in obvious ways. Effective technicians approach issues methodically, using logical analysis to isolate problems. They might start with symptoms and systematically eliminate potential causes using testing tools and inspection. This skill demands patience and creativity—sometimes issues arise from combinations of minor faults rather than a single cause. Diagnosing the root problem saves time, materials, and frustration.
Use of Diagnostic Tools
A technician’s toolkit extends far beyond wrenches and screwdrivers. Multimeters, infrared thermometers, vibration analyzers, and ultrasonic detectors reveal hidden problems before visible damage appears. Knowing how to use these devices properly is critical for preventive maintenance and accurate troubleshooting. The ability to interpret data from these tools separates reactive maintenance from proactive care.
Hydraulics and Pneumatics Expertise
Many industrial machines depend on fluid power systems. Understanding how hydraulic pumps, valves, cylinders, and compressors work allows technicians to maintain pressure, flow, and control. Troubleshooting leaks, contamination, or pressure loss requires attention to detail and knowledge of system design. Pneumatics shares similar principles but involves compressed air, requiring an understanding of regulators, filters, and actuators.
Reading and Interpreting Technical Documentation
Machines come with manuals, wiring diagrams, schematics, and parts lists. Maintenance technicians spend significant time reviewing these documents to understand complex systems. Mastery of this skill means technicians can follow step-by-step repair procedures, identify part numbers quickly, and adhere to manufacturer specifications. It reduces guesswork and mistakes.
Time Management
Maintenance tasks often compete with production demands. Technicians must prioritize urgent repairs without neglecting routine checks. Balancing scheduled maintenance with emergency fixes requires planning and flexibility. Efficient use of time minimizes downtime and ensures safety standards remain intact. This skill also involves organizing tools and parts to reduce search time during repairs.
Safety Awareness
The industrial workplace contains numerous hazards. Skilled technicians recognize risks like moving machinery, electrical shock, and chemical exposure. They follow lockout/tagout procedures meticulously to prevent accidental machine start-ups. Using personal protective equipment (PPE) correctly and maintaining a clean workspace are part of keeping themselves and coworkers safe. Safety awareness also extends to identifying unsafe conditions before accidents occur.
Communication Skills
Technicians interact with operators, supervisors, and vendors. Clear communication prevents misunderstandings that can lead to errors or delays. This includes accurately reporting issues, requesting parts, and providing instructions. Effective communication also helps build trust, fostering collaboration between maintenance and production teams.
Adaptability
Industrial environments change rapidly with new technology, processes, or equipment upgrades. Technicians who adapt quickly maintain productivity during transitions. Learning new software for computerized maintenance management systems (CMMS) or adjusting to automated machinery requires an open mind and willingness to acquire new skills. Adaptability reduces resistance to change and encourages continuous improvement.
Purchasing industrial supplies for maintenance means recognizing the value of technicians who excel in these areas. A well-rounded skill set ensures machines run longer and safer, cutting costs and boosting efficiency. Whether it’s spotting a mechanical fault, using diagnostic technology, or communicating effectively with the team, these skills define the backbone of industrial upkeep.
Industrial supply buyers can take satisfaction knowing the right tools and equipment support technicians who are ready for the challenges that come with maintaining complex systems. The investment in quality parts and training pays off when downtime shrinks and operations hum along reliably.
Here’s to the unsung heroes behind the scenes — maintenance technicians whose skill keeps everything turning without a hitch. They might not wear capes, but their expertise is nothing short of superpowers in the industrial world.